Das produzierende Gewerbe ist einer der größten Verursacher von CO₂-Emissionen und steht für ca. 31 % des Primärenergiebedarfs. In der industriellen Fertigung könnten bei einer beschleunigten Digitalisierung bis zu 12,7 Millionen Tonnen CO2 eingespart werden[1]. Genau mit dieser Aufgabenstellung befasst sich auch das vom Fraunhofer IESE geleitete Forschungsprojekt »greenProd«. In diesem Blog-Beitrag wird die Projektvision vorgestellt und bestimmte Teile des Projekts wie auch die Hintergedanken um deren Aufbau werden näher erläutert.
Das Projekt »greenProd«
Die Vision des Projekts ist es, die Transformation der produzierenden Industrie zu unterstützen und die Nutzung von Energie aus regenerativen Energiequellen zu maximieren. Dies birgt nicht nur das Potenzial, durch die Reduzierung der Nutzung fossiler Energien die Emissionen von Treibhausgasen zu senken, sondern auch die Kosten für Energie in den Betrieben zu senken und somit die Wettbewerbsfähigkeit zu steigern. Zur Umsetzung dieses Ziels werden grüne digitale Energiezwillinge (gDEZ) entwickelt. Verwaltungsschalen (Asset Administration Shells) realisieren gDEZ für Produktionsschritte, Produkte und Schnittstellen sowie gDEZ zur Verfügbarkeit von regenerativer Energie, mit denen auftretende Emissionen erfasst und zugeordnet werden können. Weiterhin beschreiben sie den Energieverbrauch bestimmter Schritte, den CO₂-Fußabdruck des Energiemixes und stellen Vorhersagen für die Verfügbarkeit erneuerbarer Energien zur Verfügung. Dies ermöglicht ein umfangreiches Tracking des CO₂-Fußabdrucks über alle Schritte hinweg. GDEZ ermöglichen Messbarkeit und Vergleichbarkeit. Somit könnte beispielsweise ein Kunde verschiedene Produkte miteinander vergleichen, oder der Hersteller selbst kann Optimierungen durchführen.
Optimierungspotenziale
Die gesammelten Daten können dazu genutzt werden, Entscheidungen zu treffen, um beispielsweise den Produktionsablauf zu verbessern. Ein möglicher Ansatzpunkt hierzu sind Investitionsentscheidungen, wo durch Kenntnis des energetischen Anteils in der Produktionskette Effizienzkriterien stärker berücksichtigt werden können. Eine andere Option ist, unter Berücksichtigung der Produktionsauslastung und der Liefertermine die Fertigungsgeschwindigkeit anzupassen. Ein denkbarer Fall hierzu wäre eine Pumpanwendung, bei der die Pumpendrehzahl so eingestellt wird, dass die Pumpe nicht im Wechselbetrieb, sondern mit konstanter Drehzahl im höheren Effizienzbereich betrieben wird. Eine weitere Option wäre, wo möglich, die Fertigungsgeschwindigkeit von Maschinen so anzupassen, dass diese möglichst effizient laufen. Die Auswirkungen sind im Anschluss anhand der Daten im gDEZ ablesbar.
Planung einer energieoptimierten Produktion
Eine weitere Optimierungsmöglichkeit liegt in der Ablaufplanung der Produktion. Hierzu stelle man sich eine Fabrikhalle vor: Es gibt unterschiedliche Produktionsschritte, welche bestimmte Produkte durchlaufen müssen. Jedoch sind nicht alle Maschinen zu jeden Zeitpunkt voll ausgelastet, und nicht jeder Prozess benötigt dieselbe Menge an Energie. Wenn man es schafft, diejenigen Prozesse, die besonders viel Energie benötigen, dann auszuführen, wenn besonders viele erneuerbare Energien verfügbar sind, wird der CO₂-Fußabdruck reduziert. Dies hat sogar einen erfreulichen Nebeneffekt: Da die erneuerbaren Kraftwerke die besonders kostenintensiven Erzeuger, beispielsweise Gaskraftwerke, aus dem Markt drängen, sinkt zu diesem Zeitpunkt der Börsenstrompreis. Besitzt das Unternehmen einen flexiblen Stromtarif oder kauft seinen Strom selbst an der Börse, entsteht hierdurch automatisch ein Kostenvorteil. Dieser Teilaspekt wird im Folgenden genauer betrachtet.
Umgebungsmodell
Zunächst muss die Produktionsumgebung abstrahiert und modelliert werden. Eine Möglichkeit hierzu ist, den Produktionsablauf eines jeden Produkts als eine Abfolge von Verarbeitungsschritten anzusehen. Diese Schritte erfolgen sequenziell und sind untereinander nicht austauschbar. Will man beispielsweise ein Gewinde in ein Werkstück schneiden, so muss man zunächst das Werkstück auslagern, dann bohren und anschließend schneiden. Bohren und Gewindeschneiden stellen hierbei jeweils einen konkreten Prozessschritt dar. Die jeweils eingesetzten Maschinen können hierbei identisch sein, müssen es jedoch nicht. Für das Fabrikmodell bedeutet dies, dass man jedem Prozessschritt Maschinen zuordnet, wobei eine Maschine auch mehreren Schritten zugeordnet werden kann. Weiterhin können am Ende unterschiedliche Werkstücke auf denselben Prozessschritt warten (beispielsweise das Bohren), sodass es zu Wartezeiten kommt. Dies wird im Modell mittels einer »Warteschlange« für den jeweiligen Schritt abgebildet.
Auftragsmodellierung
Mit diesen Elementen ist es bereits möglich, eine Produktionsumgebung zu beschreiben, jedoch fehlen zur Darstellung des Produktionsablaufs wichtige Produktinformationen. So ist zwingend erforderlich zu wissen, was überhaupt hergestellt werden soll und welche Schritte dazu erforderlich sind. Da in einer Fabrik für gewöhnlich nicht manufakturähnlich Einzelstücke produziert werden, sondern gewisse Stückzahlen, kann man diese Informationen in sogenannten Betriebsaufträgen zusammenfassen. Ein Betriebsauftrag ist hierbei etwas vereinfacht gesagt eine Art interne Bestellung für ein konkretes Produkt oder aber auch ein selbst produziertes Teil. Durch die Zerlegung der Kundenaufträge in Betriebsaufträge können Überschneidungen ausgenutzt werden, und der gesamte Produktionsprozess kann im internen ERP-System abgebildet werden. Zur Verdeutlichung ein Exempel:
Bestellen zwei Kunden unterschiedliche Produkte, etwa ein Fenster mit den Maßen 100×100 cm und eins in der Größe 80×80 cm, so unterschieden sich Teile der Produktion und führen zu unterschiedlichen Betriebsaufträgen bei der Rahmenfertigung. In dem Beispiel würden die Rahmenteile auf eine unterschiedliche Größe geschnitten. Andere Teile hingegen, wie der Griff oder die Scharniere, sind identisch. Deren Produktion würde in Betriebsaufträgen zusammengefasst.Ziel dieses Zusammenfassens ist es, die Standzeiten der Maschinen (bspw. verursacht durch Transport- oder Rüstzeiten) zu reduzieren und effizienter zu arbeiten. Auch dies muss im Modell entsprechend abgebildet werden. Um Synergien zwischen Aufträgen zu finden, gibt es bereits etablierte Prozesse in den Unternehmen, sodass für das Modell die Betriebsaufträge als Ausgangspunkt für die Optimierung der Produktionsplanung dienen.
Abhängigkeiten
Ein wichtiger Punkt bei der Abbildung der Betriebsaufträge ist die Berücksichtigung der möglichen Abhängigkeiten. Aufeinanderfolgende Schritte innerhalb eines Auftrags stellen die einfachste Form von Abhängigkeit dar. Es können wie im Fensterbeispiel (beide warten auf den Griff) auch zwei Aufträge einen gemeinsamen, vorausgesetzten Auftrag besitzen. Dieser wird als eigener Auftrag abgebildet, während die davon abhängigen Aufträge zurückgestellt werden müssen. Ebenso kann ein Auftrag von mehreren Voraufträgen abhängig sein (ein Fenster benötigt einen Griff und Scharniere). Auch alle Kombinationen sind möglich.
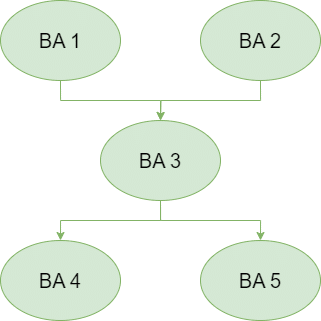
Nutzung des Modells
Das so konzipierte Modell, welches all diese Aspekte berücksichtigt und zu den genannten Komponenten noch Eigenschaften wie Standbyverbrauch, Leistungsaufnahme im Betrieb, Rüst-, Nutzungs- oder Durchlaufzeiten berücksichtigt, kann vereinfacht wie folgt dargestellt werden.
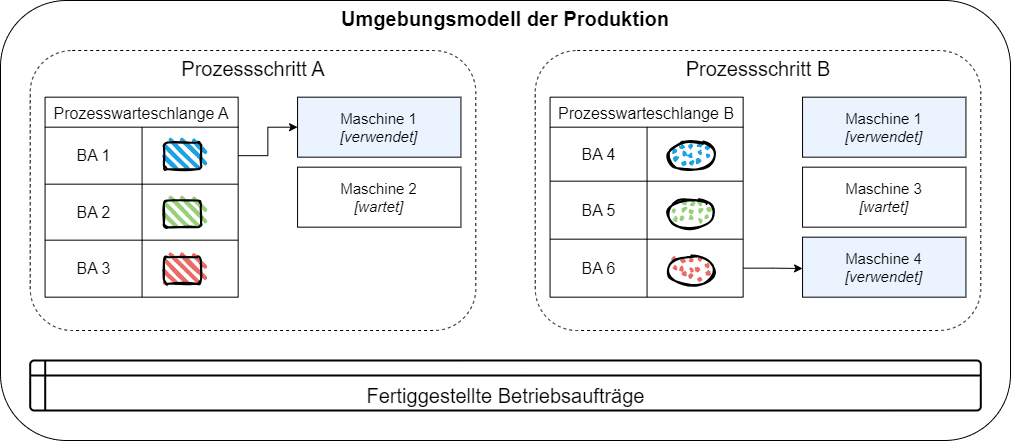
Im Projekt wird dieses Modell nun mit einem Scheduler und einer Simulationssteuerung gekoppelt, um eine Monte-Carlo-Simulation durchzuführen. Bei einer solchen Simulation werden bestimmte Entscheidungen zufällig getroffen, um bestimmte Zeiträume zu simulieren. Hierzu gehört beispielsweise das Scheduling, also die Planung der Produktionsabläufe. Hierzu betrachtet der Scheduler die Warteschlange und die freien Maschinen eines Prozessschritts und trifft eine Entscheidung darüber, ob und welcher Auftrag einer Maschine zugeordnet wird. Das Modell simuliert dann die Bearbeitung und verwaltet die Aufträge. Die Simulation erfolgt grundsätzlich zeitbasiert in äquidistanten Zeitschritten bis zu einem eingestellten Endzeitpunkt. Am Ende wird das Ergebnis hinsichtlich ökonomischer sowie ökologischer Kenndaten ausgewertet und der beste Ablaufplan wird vorgeschlagen. Zu den Kriterien gehören beispielsweise Einhaltung von Deadlines, Maschinenauslastung, Energieverbrauch, Energiekosten oder auch CO₂-Emissionen.